If you choose NRND or EOL components due to oversight, you could face losses of tens of thousands of dollars, or worse, your product might never reach the market. Sounds alarming, right? As a hardware entrepreneur, understanding the product status of electronic components is essential for managing risks and controlling costs in mass production.You can also click here to watch the YouTube video.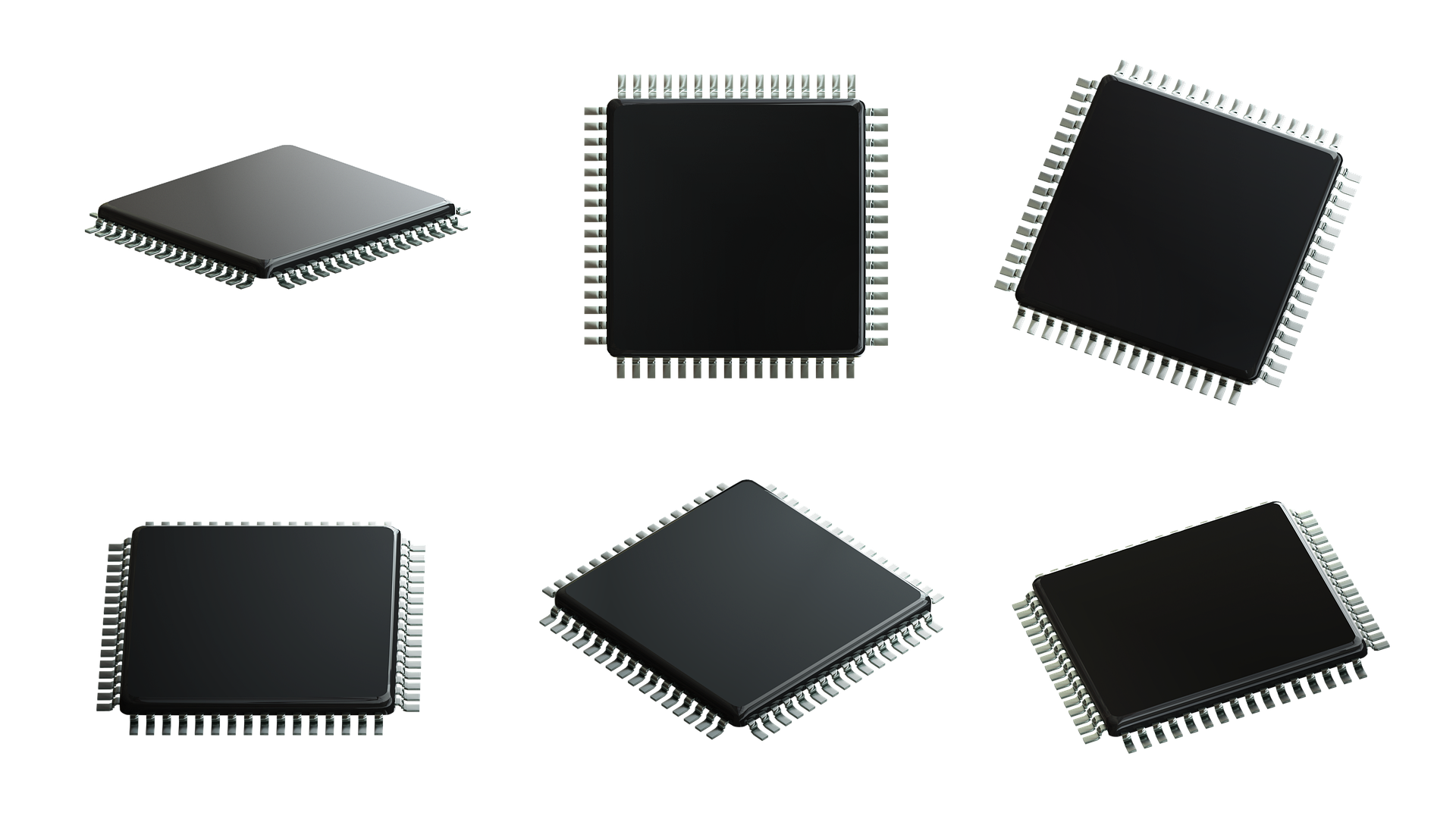
I’d like to share some critical insights into how the product status of components can affect your manufacturing journey and, more importantly, what you can do to mitigate these challenges.
Understanding Component Product Status
The "product status" of electronic components refers to their life cycle stage in the market. Here’s a quick breakdown:
- Preview: Not in full production, but experimental parts are available.
- Active: Currently in production and widely available.
- NRND (Not Recommended for New Designs): Still in production but nearing the end of its life cycle.
- EOL (End-of-Life): No longer in production, limited to distributor stock.
- Obsolete: Completely discontinued, no stock available.
Generally, industrial components remain active for 10-15 years, while consumer components have shorter life spans of 3-5 years. Understanding where a component stands in its life cycle is crucial for managing costs and production risks.
How Product Status Affects Manufacturing Costs
- Availability and Rising Costs
Active components are usually cost-effective due to their high production volumes and steady availability. However, once a component transitions to NRND or EOL, availability drops, and prices soar. Why?
- Stock in the supply chain becomes limited.
- Companies using the same components rush to secure what’s left.
This drives up your BOM (Bill of Materials) costs significantly.
- Unpredictable Lead Times and Quality Risks
Active components typically have predictable lead times of 4-12 weeks. But as a component approaches EOL, lead times can vary greatly, sometimes extending by months. This can:
- Delay your production schedule.
- Force you to purchase from brokers or alternative sources at inflated prices, increasing the risk of counterfeit or substandard parts.
Using such components may compromise quality, leading to costly recalls or warranty claims.
- Changes in MOQs (Minimum Order Quantities)
EOL components often come with higher MOQs, as brokers prefer not to store small quantities in their warehouses. This could force you to purchase far more than needed, resulting in unnecessary inventory costs.
- Expensive Redesigns
If a critical component becomes unavailable, redesigning your product may be the only option. Redesigns involve costs like new prototypes, updated certifications, and engineering hours, which can delay your time-to-market and hurt profit margins.
How to Manage Risks as a Hardware Entrepreneur
Managing component product status might seem daunting, especially for small teams. However, implementing even one of these strategies can make a significant difference. If this seems overwhelming, consider partnering with a turnkey manufacturer like NexPCB, which has extensive supply chain experience to mitigate risks for you.
- Design for Longevity
- Select components with long life cycles during the design phase.
- Check manufacturers’ roadmaps to ensure critical components stay active throughout your product’s life span.
- If your design relies on open-source solutions, always use the latest version.
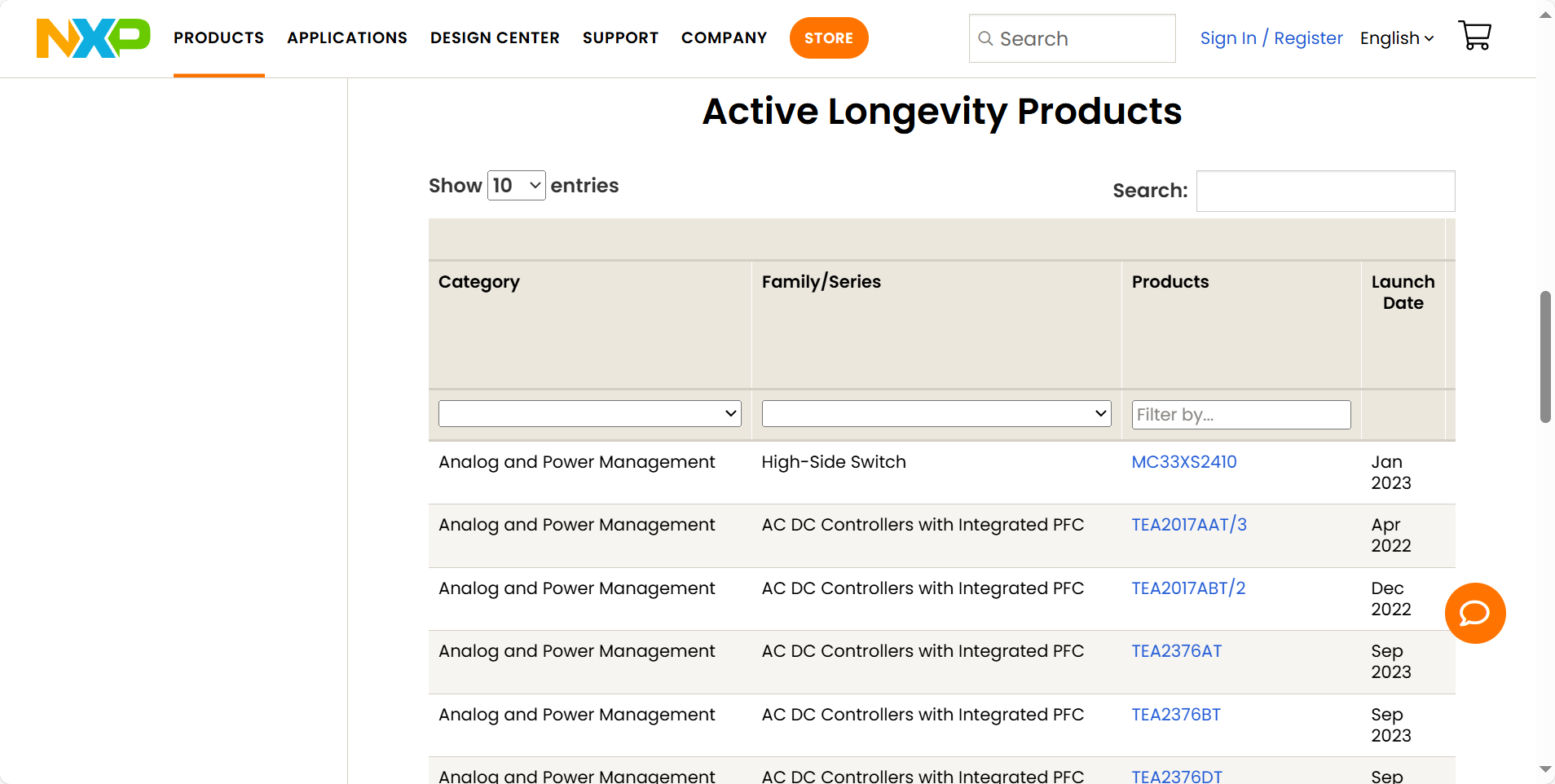
- Monitor Component Status Regularly
Use online tools and suppliers to track changes in the status of components in your BOM. For example:
- Classify components as regular, concern, or critical based on price and supply.
- Monitor critical components weekly or even daily, while observing regular components every six months.
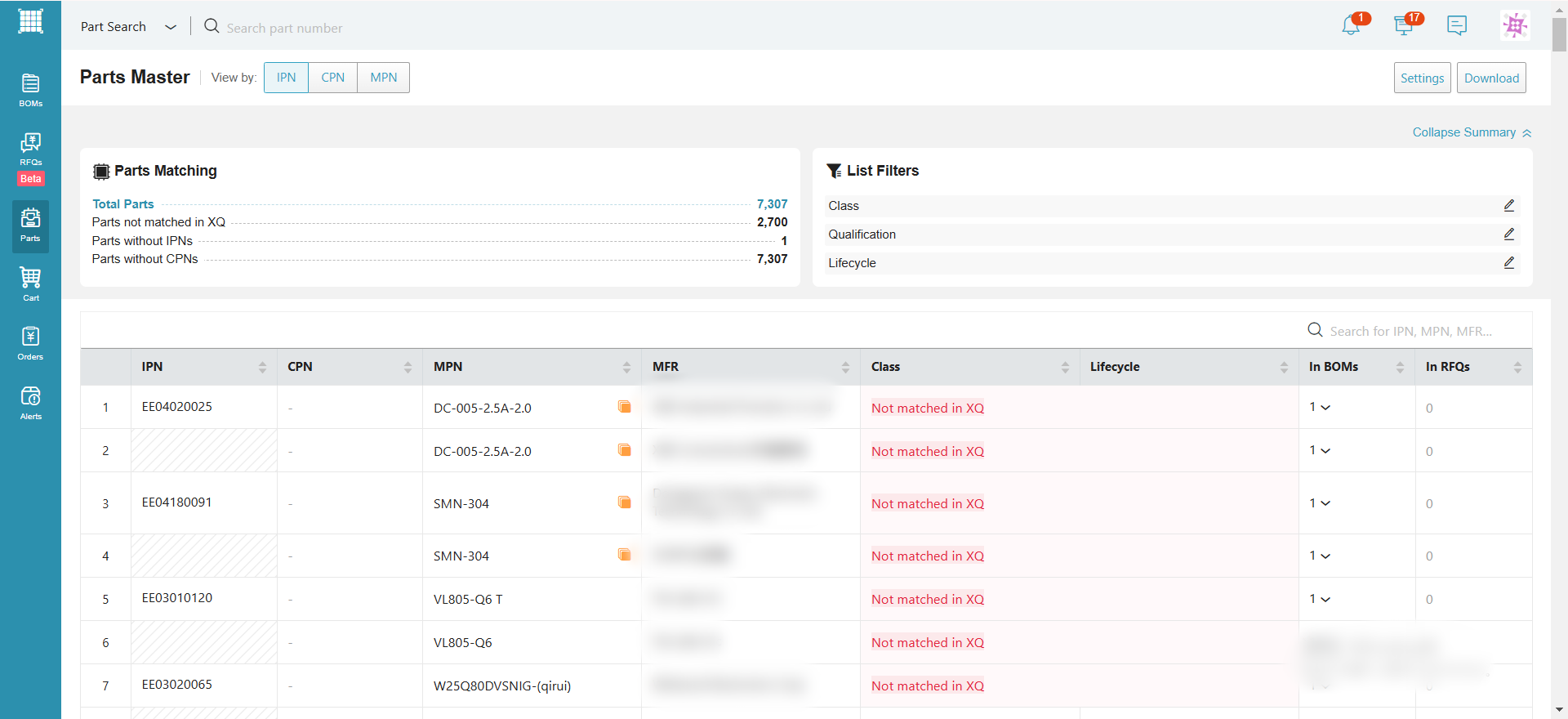
- Build Strong Supplier Relationships
Partner with reliable suppliers who can help you secure stock at reasonable prices, even for components nearing EOL. Suppliers like Rochester Electronics specialize in sourcing such components.
- Maintain a Safety Stock
This is one of the most effective strategies. For critical components, consider:
- Preparing enough for the next production batch.
- Maintaining stock for six months or more.
- Reserving components for the entire product life cycle (for products with high profit margins).
This strategy reduces supply chain risks but may result in some inventory waste, so balance it with your development stage and margins.
Final Thoughts
The product status of electronic components plays a pivotal role in determining the cost and success of mass manufacturing. By staying proactive and implementing strategies like designing for longevity, monitoring component status, and maintaining a safety stock, you can avoid costly redesigns and delays while keeping production costs under control.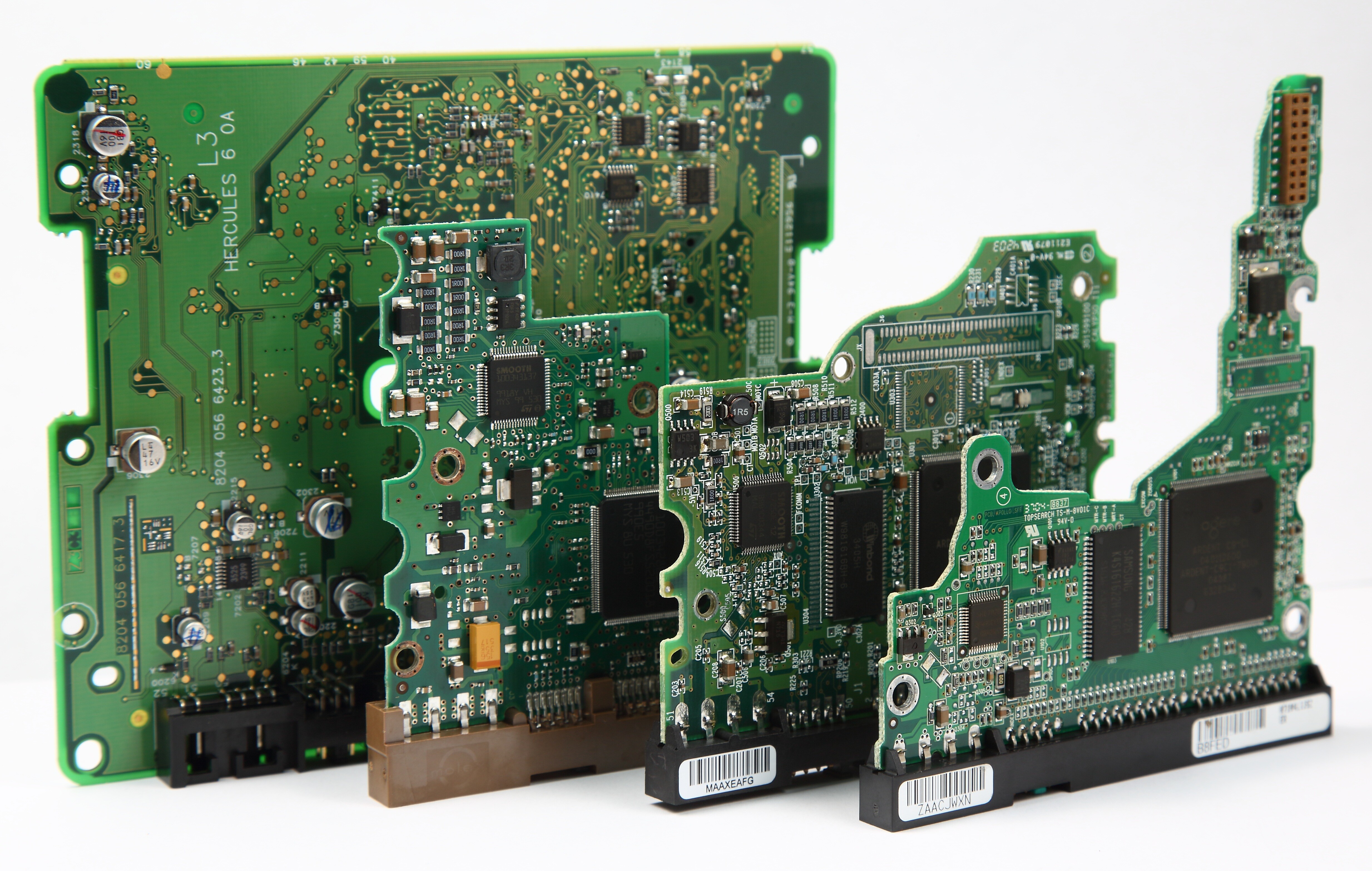
At NexPCB, we’ve helped countless entrepreneurs navigate these challenges, and we’re here to help you too. Have you faced issues with component availability or rising costs? Share your story in the comments below.
Thanks for reading, and stay tuned for more insights on hardware development and supply chain management! 🚀